What is Porosity in Welding: Key Factors and Their Impact on Weld Top Quality
What is Porosity in Welding: Key Factors and Their Impact on Weld Top Quality
Blog Article
Porosity in Welding: Identifying Common Issues and Implementing Best Practices for Prevention
Porosity in welding is a prevalent concern that typically goes undetected until it creates considerable issues with the honesty of welds. In this conversation, we will check out the key variables adding to porosity development, examine its harmful results on weld efficiency, and go over the ideal methods that can be embraced to decrease porosity occurrence in welding processes.
Common Reasons of Porosity
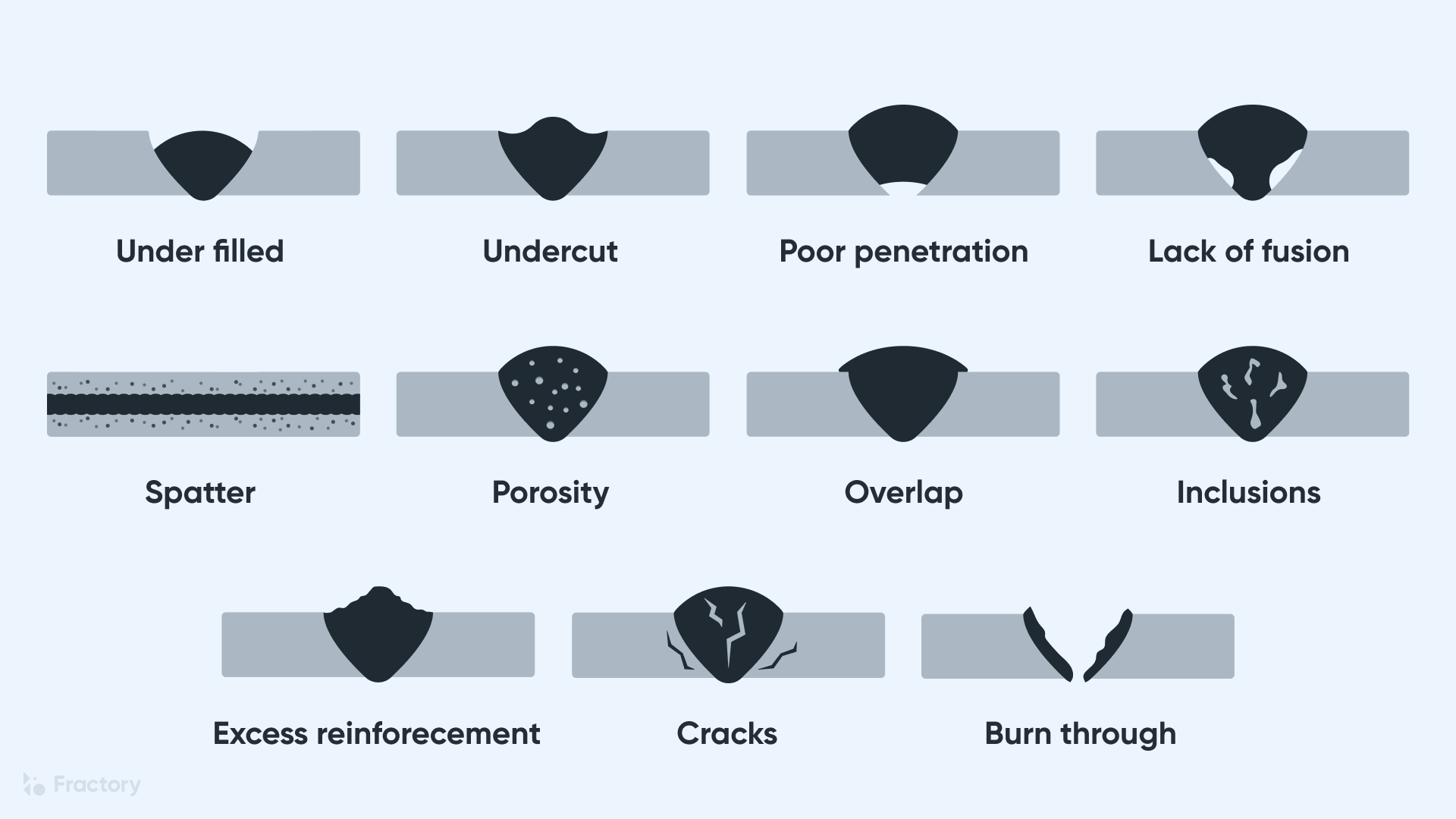
An additional frequent culprit behind porosity is the visibility of pollutants externally of the base metal, such as oil, oil, or rust. When these contaminants are not effectively eliminated prior to welding, they can evaporate and come to be trapped in the weld, triggering issues. Utilizing unclean or damp filler products can present contaminations right into the weld, contributing to porosity concerns. To mitigate these common root causes of porosity, thorough cleaning of base steels, appropriate protecting gas choice, and adherence to ideal welding parameters are crucial practices in achieving premium, porosity-free welds.
Influence of Porosity on Weld Top Quality

The presence of porosity in welding can considerably jeopardize the architectural integrity and mechanical homes of bonded joints. Porosity develops voids within the weld metal, damaging its overall toughness and load-bearing capability. These voids act as tension focus factors, making the weld more vulnerable to fracturing and failure under used loads. Furthermore, porosity can decrease the weld's resistance to corrosion and various other ecological variables, further diminishing its longevity and efficiency.
One of the key repercussions of porosity is a decline in the weld's ductility and durability. Welds with high porosity degrees have a tendency to exhibit lower impact toughness and lowered capability to deform plastically prior to fracturing. This can be particularly worrying in applications where the welded components are subjected to vibrant or cyclic loading problems. Additionally, porosity can hinder the weld's capability to successfully transmit pressures, causing premature weld failure and prospective security risks in essential structures.
Best Practices for Porosity Avoidance
To improve the structural honesty and top quality of welded joints, what certain actions can be executed to lessen the event of porosity throughout the welding procedure? Utilizing the proper welding technique for the particular material being bonded, such as changing the welding angle and weapon placement, can further prevent porosity. Regular assessment of welds and prompt removal of any kind of concerns determined throughout the welding procedure are crucial techniques to protect against porosity and produce top quality welds.
Value of Appropriate Welding Methods
Carrying out correct welding strategies is vital in making certain the architectural honesty and top quality of bonded joints, go to my blog building on the structure of efficient porosity prevention steps. Welding strategies directly impact the total toughness and resilience of the welded framework. One vital facet of appropriate welding techniques is preserving the appropriate heat input. Excessive warmth can cause boosted porosity due to the entrapment of gases in the weld swimming pool. Alternatively, not enough warm may cause insufficient combination, creating possible weak factors in the joint. Furthermore, using the ideal welding specifications, such as voltage, current, and take a trip rate, is important for achieving audio welds with very little porosity.
In addition, the selection of welding procedure, whether it be MIG, TIG, or stick welding, ought to align with the specific needs of the job to make sure optimal results. Correct cleaning and preparation of the base steel, as well as choosing the appropriate filler material, are likewise necessary elements of competent welding techniques. By sticking to these finest practices, welders can lessen the danger of porosity formation and create premium, structurally audio welds.

Testing and Quality Assurance Actions
Quality assurance steps play an essential duty in confirming the integrity and integrity of bonded joints. Testing treatments are important to discover and protect against porosity in welding, ensuring the strength and toughness of the end product. Non-destructive screening methods such as ultrasonic testing, radiographic testing, and visual evaluation are frequently used to recognize possible issues like porosity. These techniques permit the evaluation of weld high quality without jeopardizing the stability of the joint. What is Porosity.
Post-weld assessments, on the other hand, analyze the final weld for any type of issues, including porosity, and verify that it fulfills defined standards. Carrying out a comprehensive high quality control strategy that consists of extensive screening treatments and inspections is extremely important to decreasing porosity problems and making certain the overall high quality of bonded joints.
Verdict
Finally, porosity in welding can be a common problem that affects the top quality of welds. By identifying the common sources of porosity and carrying out finest techniques for avoidance, such as proper welding methods and testing actions, welders can make certain high quality and reliable welds. It is vital to prioritize avoidance techniques to you could try this out decrease the you could try this out incident of porosity and maintain the stability of welded frameworks.
Report this page